Nicon Oculon T02 Focus Not Working and Whats inside it?
The Nicon Oculon T02 is a piece of optical equipment that promises performance, precision, and durability for astronomy, birdwatching, and a wide range of observational pursuits. Many consumers choose this model for its purported reliability and the reputation of the Nikon brand, which has been known for decades to produce high-quality cameras, lenses, and binoculars. However, some users have reported focus malfunctions—most notably in the left eyepiece—causing them to question both the craftsmanship and the choice of internal materials. When the focus mechanism fails, it can be disheartening, especially if the device has been in use for only a relatively short time.The experience of discovering a broken plastic component within a binocular that is otherwise encased in a robust aluminum alloy shell raises pertinent questions about design choices, manufacturing processes, and the broader concept of planned obsolescence. This article examines the internal components of the Nicon Oculon T02, focusing particularly on the plastic part responsible for left-eye focusing. It also delves into engineering aspects of optical instruments, the nature of materials used in such products, and potential long-term implications for consumer trust. The overall aim is to provide a detailed exploration of why this broken plastic piece might be considered a critical point of failure, how such failures align with or differ from industry standards, and what might be gleaned from examining the device’s interior construction.

External Construction and First Impressions
From the outside, the Nicon Oculon T02 exudes a sense of premium quality. The body is typically described as made of a die-cast aluminum alloy, which suggests structural integrity and longevity. The surface usually has some form of rubberized coating, ostensibly to enhance grip and protect against minor bumps or abrasions. When held, the binocular feels balanced in the hands, a factor often cited as an important ergonomic element for extended use. Such external traits help the product appeal to a range of users, from hobbyists to professional observers.Marketing materials emphasize ruggedness, water resistance, and optical clarity. The binoculars may also come with nitrogen purging to reduce internal fogging and O-ring seals for water resistance. These aspects contribute to an image of durability and reliability, which often justifies a higher price point. Such features also signal an expectation among buyers: if the external and optical qualities appear robust, then the internal mechanics—particularly the focusing assembly—would presumably match this high standard. Yet, as user experiences and the subsequent disassembly revealed, the internal choices of materials may be at odds with the robust exterior.
Focus Mechanism and Observed Failure
One of the most crucial parts of binocular functionality is the focusing mechanism. For the Nicon Oculon T02, this mechanism typically involves:- A central focus knob or wheel that adjusts both barrels simultaneously.
- A diopter adjustment ring, usually on the right or left eyepiece, to fine-tune focus for visual differences between the user’s left and right eyes.
- A series of gears and linkages that translate turning motions into shifts in the internal lens groups or ocular assemblies.
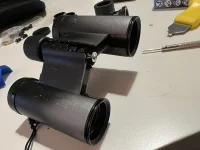
The focus mechanism on the left eyepiece in question ceased to function properly, rendering the binocular effectively unusable for that eye. Upon opening the device, a broken plastic component was discovered. This piece appeared to connect the focusing wheel’s motion to the ocular lens assembly, ensuring that minute rotations corresponded to subtle changes in lens positioning. The exact nature of the plastic part varied based on the user’s description and photographic evidence, but it was consistently identified as a crucial pivot or gear that enables smooth focusing.
The fact that the binocular was only about a year old before failure raises concerns about reliability. The optics remained undamaged, and no external part of the binocular showed signs of undue wear or stress, which points to an internal fault likely associated with either a manufacturing defect or a systematic design choice—namely the usage of plastic in a part that endures mechanical stress.
Why Plastic Components in a Metal Housing?
In engineering and product design, the choice to integrate plastic components within a metal chassis can serve several functions:- Cost Reduction: Plastic is often less expensive than metal when it comes to both material and manufacturing processes.
- Weight Savings: While aluminum alloys are relatively lightweight, certain types of plastics are even lighter, reducing the overall weight of the product.
- Ease of Manufacture: Plastic can be molded into complex shapes more easily than metals, potentially streamlining production.
- Noise Reduction: Plastic gears can run more quietly than metal gears, minimizing unwanted sounds during focusing.
However, if not properly reinforced or selected with sufficient durability, plastic can become a weak link in an otherwise robust design. This can lead to:
- Early Wear and Tear: Plastic gears may degrade or strip faster than their metal counterparts.
- Thermal Sensitivity: Plastic can be more susceptible to temperature extremes, leading to expansion or brittleness.
- Fragility Under Shock: A forceful impact that might be absorbed by metal could crack or break a plastic part.
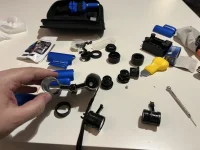
In the case of the Nicon Oculon T02, the mismatch between a die-cast aluminum exterior and an essential plastic focusing component raises questions about whether the materials align with the binocular’s premium image. Owners may feel misled if the marketing emphasized ruggedness without disclosing the presence of vulnerable plastic parts in critical areas.
Inside the Nicon Oculon T02: A Closer Look
Upon opening the binocular’s body, certain components become visible:- Optical Prisms: Typically high-quality Porro or roof prisms, depending on the model variant, designed to correct the inverted image formed by objective lenses.
- Objective Lenses: Often made of multi-coated glass to maximize light transmission and minimize aberrations.
- Focusing Assembly: A small system of gears, rods, and rings that adjust the distance of the ocular lenses relative to the objective lenses.
- Diopter Adjustment Mechanism: Another set of small gears or cams, often with incremental markers to match individual eyesight differences.
- Internal Housing and Mounts: Aluminum or plastic frames that hold the optical components in alignment.
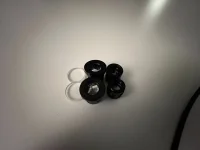
In the Oculon T02 specifically, photographs of disassembled units indicate a primarily metal interior for the critical optical pathways. Most of the structure that keeps the prisms and lenses in place is made of metal or rigid polymers designed for stability. However, the focus gear assembly can include plastic gears, rings, or coupling arms. One of these plastic components—sometimes a small gear or bracket—bears the brunt of the mechanical action when users rotate the focus knob. If it snaps, focus on one or both eyepieces ceases to function.
Potential Causes of Plastic Component Failure
Several factors can lead to breakage in plastic parts subjected to mechanical stress:- Manufacturing Defects: Inconsistent material mixtures, insufficient curing times, or contamination during the molding process can result in weak spots.
- Design Flaws: A geometry that concentrates stress in a thin cross-section or a pivot point can predispose the part to cracking.
- Environmental Stress: Extreme cold or heat can weaken the plastic. Repeated expansion and contraction cycles might cause micro-fractures over time.
- User Handling: Rough handling, drops, or incorrect usage can exacerbate stress on fragile parts.
For the user who experienced the focus malfunction within a year, none of the above typically “expected” conditions—such as severe drops or harsh environmental exposure—were reported. Hence, suspicion often falls upon the inherent fragility of the design or a potential manufacturing flaw. Further compounding the issue is the discovery that opening the binocular voids the warranty. Even if the breakage is a result of flawed design, consumer protection is often forfeited once the internal assembly is accessed by the user.
Examining Planned Obsolescence in Optical Devices
The presence of a plastic focusing part inside an otherwise sturdy binocular has led some to argue that this design choice could be a form of planned obsolescence. Planned obsolescence is a strategy where products are designed to have a limited lifespan, encouraging replacement or upgrade within a predetermined time frame. While not exclusive to binoculars, it is often cited in electronic devices, automobiles, and appliances. In optical equipment, however, the concept is more contentious, given that many enthusiasts expect binoculars, telescopes, and camera lenses to last for decades if well cared for.Arguments supporting the planned obsolescence theory:
- Strategic Material Use: The substitution of metal with plastic in high-stress components can shorten the product’s functional life.
- Repair Complexity: Voiding the warranty upon disassembly discourages self-repair or third-party repair, pushing consumers toward replacing the product entirely.
- Profit Motive: Manufacturers may benefit financially from repeat purchases if products fail shortly after their warranties expire.
Arguments against the planned obsolescence theory:
- Cost-Benefit Trade-Off: Using plastic may be intended to keep the device affordable while maintaining optical performance.
- Lightweight Necessities: For handheld optical devices, weight is a factor in user comfort. Carefully chosen plastics can be both strong and lightweight.
- Manufacturing Practicalities: Complex metal parts can be more difficult and expensive to produce with the needed precision.
It is difficult to draw a definitive conclusion without more data on average lifespans, failure rates, and the specific engineering reasoning behind these plastic choices. Nonetheless, the suspicion among some consumers remains, particularly because the broken piece directly affects core functionality.
Mechanical Stress Analysis in Binoculars
Focus mechanisms involve small gears and precise movements. Even minor discrepancies in gear alignment can cause uneven stress distribution. When certain parts are plastic, repeated use can lead to gradual deformation—sometimes not immediately visible to the naked eye. Over time, such deformation may either suddenly manifest as a crack or lead to an incremental loss of precision in focus.In well-designed systems, plastic gears can function for tens of thousands of cycles without issue, particularly if they are made of engineering plastics such as polyoxymethylene (POM), nylon variants, or reinforced composites. Key considerations include:
- Gear Tooth Profile: The shape and size of each tooth must distribute forces evenly.
- Lubrication: Proper lubricants reduce friction and prevent excessive wear.
- Thermal Behavior: The material’s coefficient of thermal expansion must be compatible with the surrounding metal parts.
- Thickness and Support: Thicker sections and supportive structures can reduce stress concentrations in vital areas.
If the plastic component in the Oculon T02 was insufficiently reinforced or featured a flawed gear tooth design, it might be more prone to failure. The break might also indicate a lack of adequate testing under various conditions, such as low temperatures or repeated high-stress cycles.
Comparisons With Other Binocular Models
To place this issue in context, it can be helpful to compare how other manufacturers approach focus mechanisms. Some premium binoculars utilize full metal gear trains, while others rely on high-grade engineering plastics. The difference often lies in:- Price Range: Higher-priced models may justify the cost of metal gears.
- Brand Philosophy: Some manufacturers prioritize longevity and reputation, opting for metal throughout the mechanism.
- Technological Advancements: Reinforced plastics or hybrid metal-plastic systems can balance reliability with weight and cost constraints.
Below is a simplified table illustrating typical approaches by various price segments:
Price Segment | Focusing Mechanism Material |
---|---|
Budget Binoculars | Primarily plastic gears and housings |
Mid-Range Binoculars | Combination of metal and high-grade plastic gears |
Premium Binoculars | Mostly metal gears, sometimes with hybrid polymer elements |
Professional/Military Grade | Metal gear assemblies, extensive weather and shock resistance |
Nikon’s reputation generally places many of its models in at least the mid-range or premium category, which is why the discovery of a seemingly fragile plastic gear in the Oculon T02 focusing system may surprise many. While the brand’s marketing might emphasize premium construction, actual material choices for internal components can vary. This discrepancy underlines the importance of transparent communication and well-documented quality assurance processes.
Implications for Repair and Warranty
When encountering broken internal parts, consumers have several potential avenues:- Manufacturer Warranty: Typically covers manufacturing defects for a designated period. Opening the device without authorization often voids this warranty.
- Professional Repair: Sending the binocular to an authorized service center can be costly, and replacement parts may not be readily available.
- DIY Repair: Attempting to 3D-print or salvage a replacement plastic gear. This requires skill, tools, and likely voids any remaining warranty.
- Replacement: In cases where repair costs outweigh the value, consumers might opt to buy another pair of binoculars.
In many cases, plastic gears are customized for specific devices, making it challenging to source replacements off the shelf. The issue becomes more pronounced if the manufacturer does not supply spare parts to third-party repair shops. For consumers who demand product longevity, such obstacles can diminish brand loyalty.
Consumer Trust and Brand Reputation
Optics companies such as Nikon have cultivated reputations for excellence over many years. When a product like the Nicon Oculon T02 features a design that seemingly compromises on durability, it can create friction between brand image and consumer experience. Trust is an intangible asset that helps companies maintain loyal customers. A single flaw, especially one interpreted as indicative of broader corporate strategy, can erode that trust.In many industries, brand reputations are painstakingly built and easily tarnished. For binocular manufacturers, reliability is paramount because binoculars are often purchased for long-term use in outdoor or specialized applications. Consumers typically expect robust performance over multiple years, even decades, with only minimal maintenance. Discovering that key internal parts are prone to breakage within a short time frame can be seen as a departure from that legacy of quality.
The Role of Quality Control and Testing
Quality control in optics manufacturing extends beyond checking lenses for scratches and verifying alignment. It involves testing the longevity of mechanical components under various conditions that might include:- Temperature Extremes: Testing at very low and very high temperatures to ensure plastic components do not become brittle or warp.
- Repetitive Motion: Simulating thousands of focus adjustments to check for wear on gears.
- Shock and Vibration: Assessing how well internal components hold up during drops or transport-related stresses.
- Material Aging: Analyzing how the plastic’s properties change over time, including resistance to UV light, humidity, and chemical exposure.
A broken gear relatively early in the product’s life cycle suggests potential oversights in one or more of these areas. While every manufacturer faces the possibility of defective batches, the choice of plastic for a high-stress mechanism requires rigorous testing. If cost or time constraints limit such testing, the result may be a product that looks good on the surface but harbors a hidden vulnerability.
Inside the Binocular: Optical vs. Mechanical Complexity
Binoculars combine optical complexity—multiple lens groups, prisms, coatings—with mechanical intricacy—focus mechanisms, hinge mechanisms for adjusting interpupillary distance, and diopter settings. Many binoculars that fail often do so due to mechanical rather than optical failures. High-quality glass is less likely to degrade over the short term, barring physical damage, while plastic or lightweight metal components can bear the brunt of daily mechanical stress.In the Oculon T02, the prisms and objective lenses reportedly remain in excellent condition. The issue thus resides primarily in the mechanical interface responsible for focusing. The separation between optical brilliance and mechanical reliability underscores the importance of a holistic design philosophy. Even if the optics are top-tier, a poorly chosen mechanical component can overshadow optical excellence.
Exploring Possible Solutions
In an ideal scenario, Nikon or any other manufacturer would offer a straightforward repair pathway for such critical failures. Possibilities include:- Upgraded Spare Parts: Replacing the plastic gear with a more resilient material, potentially metal or reinforced polymer.
- Reinforced Plastic Components: If manufacturing constraints necessitate plastic, employing advanced composites or adding ribs for structural support.
- Modular Construction: Designing binoculars so that users or technicians can easily replace a focus module without dismantling the entire device.
- Extended Warranties: Providing reassurance to consumers that mechanical failures are covered, reflecting confidence in the product’s durability.
Consumers who open their devices, however, often find it difficult to secure official support. Manufacturers typically cite liability concerns and the risk of improper reassembly. Though these are valid considerations, they can also appear as deterrents that push consumers toward outright replacement rather than economical repair. For users with technical savvy, 3D printing or custom machining a replacement gear might be an option, but this approach is time-consuming and may not meet the precision standards needed for optimal focusing.
Historical Context of Plastic Use in Optical Equipment
The shift toward plastic components in optical gear is not a new phenomenon. Throughout the latter half of the 20th century, manufacturers across industries adopted engineering plastics for gears and structural parts. In some camera models, shutter mechanisms and film winding components were also partially plastic. The rationale typically combined cost savings, lighter weight, and faster production cycles. Yet, this shift was met with mixed reviews, especially among professional photographers and serious enthusiasts who had grown accustomed to the heft and durability of all-metal equipment.Over time, engineering plastics have significantly improved. Polymers such as polycarbonate, carbon-fiber reinforced nylon, and others can exhibit impressive mechanical properties. Many modern professional-grade cameras still employ a combination of magnesium-alloy chassis with internal plastic components, but these plastics tend to be carefully formulated to withstand professional-level usage. The question is whether the plastic part in the Nicon Oculon T02 meets these higher standards or belongs to a less durable category, resulting in premature failure.
User Reactions and Community Feedback
Online forums and reviews often shed light on collective user experiences. Feedback on the Nicon Oculon T02 indicates satisfaction with optical clarity, brightness, and color rendition. However, scattered reports point to mechanical issues, especially around the focus mechanism. Such reports might not be rampant, but even a few credible accounts of gear breakage can raise red flags.In many forums dedicated to binocular enthusiasts, there is a recurring piece of advice: “Try before you buy, and always check if the warranty covers mechanical faults.” Users often discuss alternative models in a similar price range, evaluating how those fare in both optics and mechanical reliability. When it comes to repair attempts, some have managed to glue cracked gears temporarily, but these fixes do not generally restore full functionality or ensure longevity.
Potential Impact on Optical Performance
A broken focusing mechanism directly impacts optical performance. Binoculars rely on precise alignment and the ability to adjust the focal plane according to the user’s eyesight and object distance. When the focus fails:- Clarity Degrades: One eyepiece or both might be stuck at an incorrect focal setting.
- User Fatigue Increases: Straining to see a sharp image leads to eye fatigue.
- Collimation Could Shift: In severe cases, a damaged internal mechanism can cause minor misalignment of the optical axes.
Even if the rest of the optical train remains pristine, the user can no longer exploit the device’s potential. This situation diminishes the value of the binocular, leaving owners with little choice but to seek repair or replace the product entirely.
Engineering Trade-Offs in Design
Designing binoculars is a balancing act of performance, cost, and user expectations. Manufacturers juggle multiple objectives:- Optical Excellence: High-quality glass, precision polishing, and advanced coatings.
- Mechanical Robustness: Durable hinges, focus mechanisms, and housing materials.
- Ergonomics and Weight: Comfort for extended viewing and portability.
- Price Point: Targeting a specific market segment with cost-effective solutions.
The use of plastic in high-stress areas suggests that cost, weight, or other considerations took precedence over maximum durability. In many industries, such compromises are acceptable if they do not undermine the user’s overall experience. However, when a critical component fails prematurely, that balance is called into question. Some might argue that additional reinforcement or alternative materials would have prevented the failure without significantly increasing manufacturing costs.
Visual Evidence and Disassembly Notes
Photographs from users who have disassembled the Nicon Oculon T02 often depict:- A compact arrangement of prisms, typically well-secured in metal brackets.
- Objective lens assemblies that slot into the aluminum housing.
- A central focusing rod connected to small gears and a diopter ring on one side.
- A plastic coupling piece that translates the rotation into linear motion for the eyepiece.
In many images, the broken piece is a small gear or coupling ring with evident stress fractures near a pivot or thin section. The fracture surfaces can sometimes appear granular, indicative of a brittle material or one that suffered fatigue stress over many focus adjustments. A more ductile plastic might have shown bending or deformation before snapping, suggesting that the chosen plastic may not have had optimal impact resistance or toughness.
User Strategies for Mitigation
Even though a broken plastic component can appear to be an irreversible problem, some users attempt to mitigate the issue:- Gentle Operation: Turning the focus wheel slowly and avoiding abrupt movements.
- Temperature Considerations: Using the binocular in moderate temperatures to reduce thermal stress on plastic gears.
- Regular Inspections: Periodically checking for signs of wear, such as unusual resistance or noise in the focus wheel.
- Protective Storage: Keeping the binocular in a padded case, away from moisture or extreme conditions.
While these measures may prolong the lifespan of a vulnerable focusing assembly, they cannot fully compensate for inherent design weaknesses. Prolonged usage in outdoor, rugged conditions can eventually exacerbate any existing flaws. For those who rely on their binoculars for professional or hobbyist pursuits, a fragile focusing system can be a significant drawback.
Industry Perspectives on Material Selection
From an industry standpoint, selecting materials involves a matrix of performance metrics. Engineers typically consult data sheets, run simulations, and perform real-world testing to ensure a chosen plastic meets the necessary criteria. Factors might include:- Tensile and Compressive Strength
- Impact Resistance
- Friction Coefficients (for gears)
- Creep and Fatigue Resistance
- Cost per Unit and Production Scalability
If a manufacturer deems plastic to be suitable for a focusing mechanism, it generally indicates that the part should endure normal operating conditions for the intended product lifespan. Failures within a short period suggest that the real-world conditions—or possibly an outlier in material batch quality—exceeded the design parameters.
Reflections on Product Lifespan
The notion that modern products have shorter lifespans is an ongoing topic of debate. While continuous innovation means newer, more advanced models appear regularly, many users prefer long-lasting products that can be serviced or upgraded. Some in the photographic and optical community have cameras or binoculars from decades past that still function well. The disappointment with the Nicon Oculon T02 arises partly because it contrasts with the historical perception of Nikon’s robust engineering.Moreover, a year of use before a mechanical failure for a mid- to high-end binocular is objectively short. Depending on usage patterns, many binoculars remain functional for years without significant issues. The fact that a simple plastic gear can curtail the product’s entire utility is unsettling for buyers who invested in what they believed to be a durable optical instrument.
Broader Context of Sustainability and Consumer Choice
Discarded electronics and optical devices contribute to global e-waste, although binoculars are not typically classed with fast-turnover items like smartphones. Nonetheless, each failure that leads to a device being junked or replaced has environmental ramifications. Consumers are increasingly mindful of product lifespans and the ease of repair. A focus mechanism that fails prematurely can thus be seen as part of a broader pattern of unsustainable manufacturing and consumption.When discussing sustainability:
- Long-lasting Products: Reduce resource usage and waste production.
- Repairability: Encourages responsible use, fosters a secondary market for parts and services.
- Brand Accountability: Companies that prioritize longevity can build strong reputations and customer loyalty.
The Nicon Oculon T02’s breakdown underscores a tension between sleek, cost-effective design and genuine sustainability. If the plastic gear could be easily replaced or upgraded, many would consider it a minor issue. However, with warranties voided upon self-disassembly and uncertain repair pathways, the device risks ending up as waste far earlier than an all-metal alternative might.
User Insights on Future Purchases
For individuals who have experienced the broken focus part in their Nicon Oculon T02, the incident could alter their approach to future purchases. Potential changes might include:- Researching Internal Mechanisms: Enthusiasts might investigate whether a particular model uses metal or plastic gears before buying.
- Examining Warranty Terms: Consumers might place greater importance on extended warranties or manufacturer repair guarantees.
- Considering Cost vs. Longevity: Some users may opt for more expensive models to avoid potential mechanical failures.
- Exploring Smaller Brands: In some cases, niche manufacturers place a premium on mechanical robustness, catering to specialized markets.
As word-of-mouth and online reviews gain traction, the experiences of a few can influence the buying decisions of many. This dynamic can motivate manufacturers to address known issues or offer improved models, although such remedies do not always arrive quickly.
Insights from a Material Science Perspective
From a materials science viewpoint, plastic can be an excellent choice for certain components when the polymer is carefully selected and properly engineered. For instance, some high-end binoculars and camera parts employ glass-fiber reinforced polyamide for gear mechanisms that function reliably under extensive use. The failure in the Nicon Oculon T02 might point to a mismatch between the chosen plastic’s properties and the stresses involved in focusing. Alternatively, even if the material selection was adequate on paper, variances in injection molding or part geometry may have led to a weak spot.Engineers often use finite element analysis (FEA) to predict where stress will concentrate in a gear design. A thorough FEA can guide the addition of reinforcing ribs or the use of fillets in corners to reduce sharp stress concentrations. If the broken gear lacked these design optimizations, it might have been more vulnerable to crack propagation. Manufacturing cost or time pressure might have limited how thoroughly the design was tested and refined.
Photographic Evidence of Internal Components
Images taken during disassembly commonly show:- The aluminum alloy frame with designated mounting points for lenses and prisms.
- Miniature screws securing the internal metal plates.
- A central shaft connected to the external focus wheel, interfacing with the now-broken gear or linkage.
- A small plastic ring or gear with sheared edges or visible cracks.
The contrast between the sturdy metal parts and the fragile plastic piece is visually striking. In many disassembled photos, everything else appears robust, reinforcing the idea that the focus mechanism’s plastic gear is the singular, albeit critical, weak link.
Evaluating Viable Repairs
While official repair might be out of reach for some, a few possible routes exist:- Epoxy or Super Glue: Attempts at gluing the broken plastic part back together typically offer only temporary relief.
- 3D Printing Replacement: Designing or scanning the broken part to create a replica in a stronger plastic or resin. Accuracy is a major challenge.
- Machined Metal Replacement: Crafting a small metal gear using CNC machining, though this is rarely cost-effective for individual repairs.
- Parts from Donor Binoculars: Finding a second broken binocular of the same model and salvaging its intact gear.
Each solution comes with caveats. Precision is paramount in a focusing mechanism; any slight misalignment will degrade optical performance. Additionally, not everyone has access to the tools or expertise for advanced repair methods. As a result, many might choose to retire the binocular.
Potential Manufacturer Responses
While the specifics of Nikon’s after-sales policies can vary by region and product line, a typical response to a mechanical failure outside of warranty might include:- Paid Repair Services: Replacing the broken components with original parts for a fee.
- Limited or No Support: Citing out-of-warranty status, especially if the user opened the device.
- Product Upgrade Path: Offering a discount on a newer model in exchange for the defective unit.
If enough consumers highlight the same mechanical problem, manufacturers sometimes issue service advisories or recall notices. Whether Nikon or related brands have taken such measures for the Oculon T02 is not broadly documented, suggesting that the problem may not be recognized on a large scale, or that the company handles such issues on a case-by-case basis.
Assessing Long-Term Reliability
Long-term reliability of the Oculon T02 and similar devices remains uncertain. Some owners may never experience the plastic gear failure, especially if they use the binocular infrequently or handle it gently. Others might encounter issues sooner if they frequently adjust the focus or expose the device to temperature extremes. The variance in individual experiences means that not all Oculon T02 units will fail, but the risk is sufficient to concern potential buyers.Reliability also depends on how thoroughly the manufacturer tested the plastic gear. Certain accelerated life tests can predict when a component might fail, providing data to refine the design before product launch. If the Oculon T02’s focus mechanism was not rigorously tested—or if the results were compromised by cost constraints—the probability of failure would inherently be higher.
Refining Design for Durability
To ensure that future models or revisions offer greater reliability, manufacturers can:- Redesign Critical Gears: Increase thickness, add support structures, or change plastic formulations.
- Adopt Metal Gears in High-Stress Areas: Reserve plastic for components that experience minimal load.
- Enhanced Quality Checks: Implement stricter inspection protocols for molded parts.
- Customer Feedback Integration: Solicit and analyze user experiences to guide design improvements.
In the competitive optics market, user reviews and brand reputation play a significant role in driving sales. Binocular enthusiasts often share detailed reviews, and any recurring mechanical failure tends to spread quickly through online communities. Manufacturers that respond proactively can restore confidence.
Balancing Cost, Weight, and Reliability
Even if a manufacturer elects to use metal gears, new challenges can arise:- Increased Weight: Metal gears add grams that, while seemingly negligible, can accumulate across multiple components.
- Higher Costs: Machining or precision casting metal gears can raise production expenses.
- Potential Noise: Metal gears may produce audible clicking or grinding if not perfectly lubricated or aligned.
In contrast, high-grade plastics can be engineered for quiet operation and minimal added weight. Therefore, the decision is not simply between plastic and metal, but rather which plastic or metal is most suitable and how thoroughly the components are tested for durability. A well-designed plastic mechanism, made with robust engineering plastics and subject to extensive testing, can rival metal in longevity for certain applications.
Critical Reflection on User Expectations
When purchasers invest in a binocular from a brand with Nikon’s standing, they might anticipate near-flawless construction. Such high expectations are partly shaped by marketing but also by the brand’s legacy in producing cameras and lenses that professionals trust. A single plastic failure, though mechanical rather than optical, can lead consumers to feel the product is subpar or intentionally designed to fail.Yet, user expectations must also be tempered by market realities. The Oculon T02 may sit in a price bracket where certain compromises are inevitable. Understanding the product’s position in Nikon’s overall lineup can provide perspective: some of the brand’s more expensive binoculars may indeed feature more robust focusing assemblies, justifying their higher cost.
Future Directions in Optical Instrument Design
Looking ahead, several trends in optical instrument design could address issues like the plastic gear malfunction:- Advanced Polymers and Composites: Continued development of materials that blend the strength of metals with the lightweight and cost benefits of plastic.
- Modular Components: Designing parts so they can be easily swapped or upgraded, encouraging repair instead of replacement.
- Smart Feedback Mechanisms: Electronic focusing aids, though more common in camera lenses than traditional binoculars, could eventually reduce mechanical stress.
- Greater Transparency: Providing detailed breakdowns of internal components so consumers can make informed decisions about longevity.
As manufacturing technologies evolve, the gap between plastic and metal performance continues to narrow. However, if manufacturers prioritize maximizing profit margins without sufficiently investing in robust design and testing, the risk of failures persists.
Visual Documentation of the Interior
Seeing the inside of the Oculon T02 reveals the interplay between meticulously arranged optics and the mechanical linkages that align them. The presence of a single plastic component that can bring the entire system to a halt underscores the importance of each part in the broader mechanism. Through such disassembly images, users can appreciate the complexity of the device—yet also identify the potential weak points.In many photos, the broken piece does not appear obviously fragile at first glance. This discrepancy highlights how intricate gear designs can harbor microscopic vulnerabilities. A slight imperfection in the molding or a subtle design flaw can remain hidden until repetitive use—over the course of months or years—causes the part to fail.
Extended Commentary on Manufacturing Economics
From a manufacturing economics perspective, opting for plastic in the focus mechanism might save a fraction of production costs per unit. When scaled to thousands of units, these savings become significant. Companies often project the device’s average usage scenario to justify such cost-saving measures. If the average user adjusts the focus wheel a limited number of times per outing, the part may be deemed sufficient. However, for power users or those subjected to harsh conditions, this calculation might not hold.Additionally, global supply chains and fluctuating metal prices can further incentivize the use of plastic. Manufacturers also face competitive pressure to keep products affordable. These economic forces can clash with user expectations for robust construction, making it challenging to deliver a product that satisfies both cost constraints and durability demands.
Consequences for Enthusiasts and Professionals
While casual birdwatchers or amateur astronomers might overlook the occasional mechanical glitch, professionals rely on consistent performance. Wildlife observers who travel extensively cannot afford to have equipment fail in the field. Those who use binoculars for research, security, or law enforcement equally depend on reliable focusing. For them, discovering a plastic part prone to failure introduces unacceptable risk, leading them to prioritize models known for all-metal construction or at least high-reliability plastic designs.Enthusiasts with engineering backgrounds sometimes see such failures as an opportunity to innovate homemade solutions. However, the majority of consumers lack the time, tools, or expertise to craft a new focusing gear. This gap between a handful of tech-savvy tinkerers and the average user highlights why manufacturer support or accessible official repairs can be pivotal.
Material Durability Testing: A Deeper Dive
Manufacturers often run standardized tests, such as the ISO 527 for tensile properties of plastics, or ASTM standards for gear testing. If the plastic used for the Oculon T02 gear was not subjected to these rigorous protocols or if the results were marginal, the part might still pass initial checks but fail under real-world conditions. Laboratory conditions can differ significantly from the varied environments in which binoculars are used. Moisture, for example, can change the mechanical properties of certain plastics, especially if they absorb water.Thermal cycling is another critical test. Binoculars used in hot deserts by day and cold nights for stargazing might see extreme temperature swings. Plastics that become brittle in the cold could crack under the stress of focusing adjustments. Without detailed transparency from the manufacturer about these tests, consumers can only speculate about whether these factors were adequately considered.
Lessons Learned
The Nicon Oculon T02 focus failure presents a case study in balancing aesthetics, cost, mechanical stress, and consumer expectations. While the product excels in optical performance and external design, a single small gear within the focus assembly remains vulnerable. The result is an uneven user experience—excellent clarity offset by potential mechanical fragility. Such incidents emphasize the value of robust design from the inside out, transparent communication about materials, and supportive after-sales services that foster consumer confidence.Beyond the technical details, this scenario reveals broader industry patterns. The tension between plastic and metal use is not merely about cost but about how well a manufacturer understands and tests the plastic’s capabilities. Users encountering a broken gear face expensive repairs and potential warranty voiding. In a market where long lifespan is an essential selling point for optical equipment, even occasional mechanical failures can carry disproportionate weight in consumer perception.
Ultimately, the broken plastic gear inside the Oculon T02 can be seen as a microcosm of the interplay between design choices and user trust. Through detailed disassembly and community feedback, the vulnerability becomes clear. Whether or not the situation constitutes planned obsolescence can be debated, but the end result—loss of functionality, frustration, and suspicions about brand integrity—remains tangible for those directly affected.
Last edited: